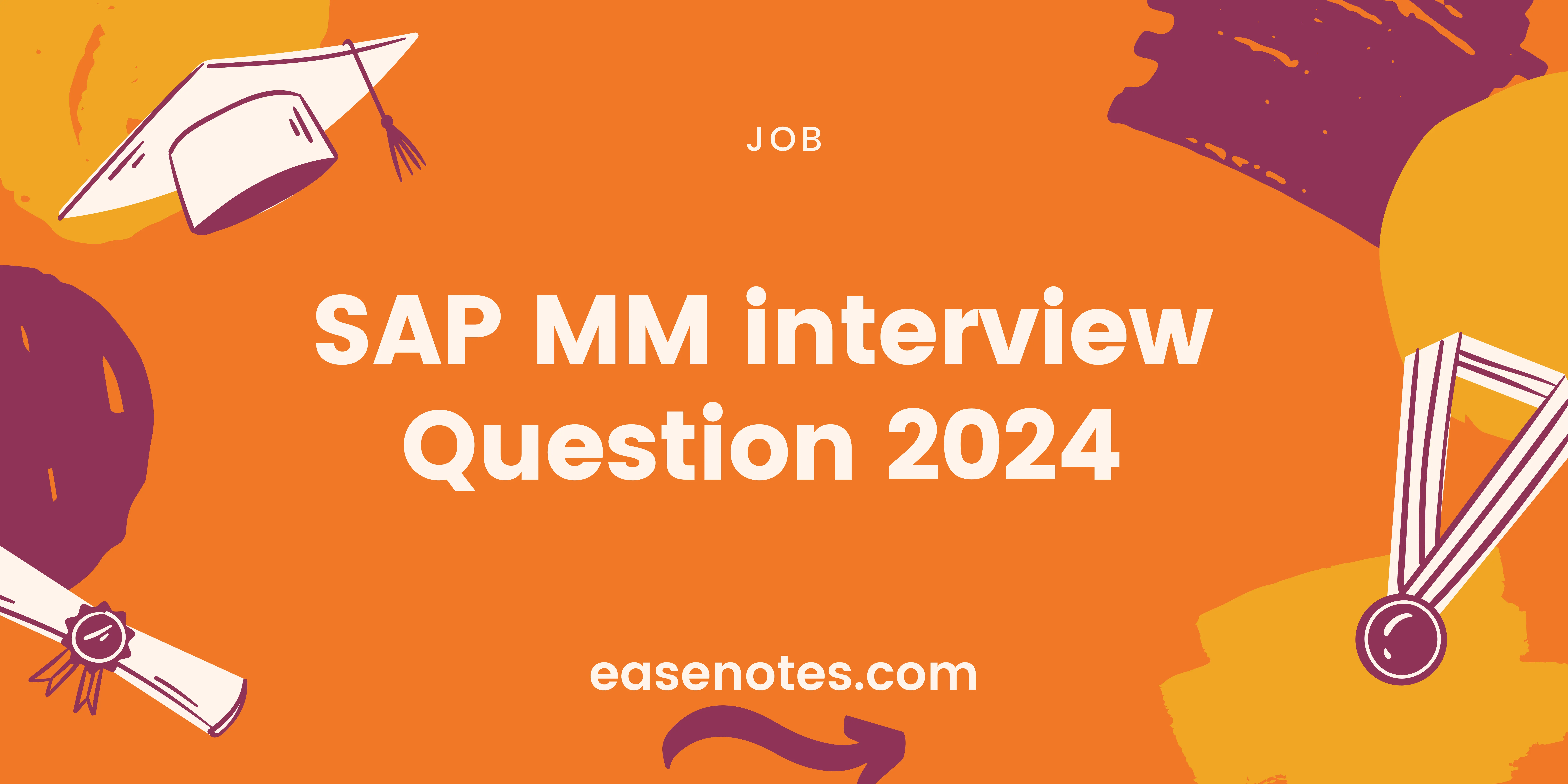
SAP MM interview Question with answers 2024
sap mm interview questions for freshers and experienced sap developers and learn frequently asked sap mm questions on companies
sap mm interview questions for freshers and experienced sap developers and learn frequently asked sap mm questions on companies. If you decide to start a career in SAP MM, you must learn SAP mm interview questions to secure a position in a good company. However, suppose you obtain a collection of SAP mm Interview questions. In that case, you can pass the SAP mm interview round regardless of whether you are a beginner or an experienced SAP developer.
Here are the top SAP MM Interview Questions
1. What is FDS, did you create it, and if created tell me the requirements?
FDS stands for Functional Design Specification, a document that outlines the functional requirements of a system.
- FDS is created by functional consultants to define the business requirements of a system
- It includes details on the system's functionality, data flow, and user interface
- FDS serves as a blueprint for developers to build the system according to the business requirements
- Example of FDS requirement: The system should allow users to create purchase orders and track their status
It has been used for 2 purposes
- 1. To create a new design
- 2. To make any changes to the existing design.
It is Go for approval in a few cases depending on the complexity of the program. Concerning this document, the logic provided by the Functional consultant ABAP team will make the required changes in the program or create the new program.
It’s with the below Heading
- FS Prepared by:
- FS version:
- FS Approved by:
- System details/Interphase details:
- Business requirement:
- AS-IS Proposed solution:
- TO-BE Functionals Specification:
- Logic Program name and tables used:
- Technical specification:
- (to be updated by Abaper) Program name and Tables used:
- UAT details:
- TR details:
- Conclusion:
2. Explain the P2P cycle in details ?
The process to pay cycle starts with procurement and ends with payment to the vendor.
- The first step is purchase requisition. PR is raised by the user department by using transaction code ME51N and sent to the purchasing department.
- The second step in Request for quotation. We create an RFQ concerning PR by using transaction code ME41N once the RFQ is created then send it to the vendor. We maintain RFQ in transaction code ME47 and compare RFQ in transaction code ME49. In transaction code ME49 we select one vendor. Against this vendor, we create a purchase order by using transaction code ME21N.
- Once the PO is created then share with the vendor. The vendor sends the material to the company. The company will receive material in the MIGO transaction along with this material vendor sends the bill, The company also checks the bill and posts it in the form of invoice verification.
- Then we verify the invoice in MIRO and share invoice documents with the Finance department and the finance department pays to vendor
The P2P cycle involves a total of 8 steps
Step 1 - Determination of Requirements
Step 2- Determination of Source of supply
Step 3 - Selection of Vendor among several [RFx]
Step 4 - Creation of PO for the selected Vendor [ ME21N]
Step 5 - Monitoring PO
Step 6 - Creation of Good Receipt [ MIGO]
Step 7 - Creation of invoice document [ MIRO]
Step 8 - Payment to the vendor
3. Explained the full process of release strategy from scratch.
Release procedure:
Purposes:
- It's used for PO approval generally, To Monitor the PO, Business Unit wise.
- The requirement PO which is an external doc, needs to be approved by L1, L2, and L3 Approval.
- SAP Release strategy is the solution.
This can be achieved by below steps.
- CEKKO-Communication table for PO Release strategy. In SAP we have a run time structure with the name CEKKO (Communication Release Strategy Determination Purch. Document) which provides all the possible lists of fields using which a release strategy can be configured.
- Configuration: Define characteristic- CT04? SPRO-MM-PUR-PO-RELESE PROCE. FOR PO-EDIT CHAR.
- In characteristic, We can have parameters like Pur. Org EKORG, doc type BSART, net PO value GNETW, currency, etc... for which PO should go for approval.
- Define class – BP Grouping the characteristic into Class CL02? SPRO-MM-PUR-PO-RELESE PROCE. FOR PO-EDIT CLASS.
- Class type 032 is mandatory Define Release strategy SPRO-MM-PUR-RELEASE PROCEDURE FOR PO-DEFINE RELEASE PROCEDURE
1. Release Group- it created BP, multiple are created in case multiple approvers are required.
2. Release Code 01,02,03 This is approver of PO ie.. L1, L2, L3
3. Release strategy (? A. Release pre-request B. Release status C. Release classification D. Release simulation classification.) Pre-Request shows the sequence of approver In release status, it's defined as PO status ie. Blocked or released. In the Release classification CLASS/RELEASE GROUP/CLASSIFICATION, synchronization can be seen. If addition values are allowed at character creation then values can be added hear.
4. Work Flow- hear with the help of ABAP WF is maintained or Release code/description/ User ID is maintained and Authorization needs to be provided for ME28 T-code.
4. What is the purchase order condition record?
The purchase order condition record is a master data in SAP MM that defines conditions for pricing and discounts in purchase orders.
-
It is used to maintain pricing conditions for materials or services in purchase orders.
-
Conditions can include discounts, surcharges, taxes, etc.
-
Condition records can be created for specific vendors, materials, or purchasing organizations.
-
They are used to automatically determine prices and discounts in purchase orders.
5. How to process inventory management
Inventory management in SAP MM involves processes like goods receipt, goods issue, physical inventory, and stock transfer.
-
Goods receipt involves receiving materials in the warehouse
-
Goods issue involves issuing materials from the warehouse
-
Physical inventory involves counting and verifying the actual stock levels
-
Stock transfer involves transferring materials between different storage locations or plants
6. What are MM -FI Config; and MM- SD Config?
MM- FI and MM-SD config is an automatic account determination process with OBYC transaction(OBYC-valuation class for mm fi), which involves material type, valuation class linked to GL accounts through account modifier.
7. What u find when u go through the transaction code me21n
ME21N is a transaction code in SAP MM used for creating a purchase order.
-
ME21N is used to create a purchase order in SAP MM.
-
It allows users to enter details such as vendor, material, quantity, and delivery date.
-
Users can also specify pricing conditions, payment terms, and delivery instructions.
-
ME21N provides options to add multiple line items and account assignments.
-
Once the purchase order is created, it can be saved, printed, or sent for approval.
8. What is consignment
Consignment is a business arrangement where a supplier retains ownership of goods until they are sold by the customer.
-
The supplier retains ownership of goods until they are sold by the customer
-
Goods are stored at the customer's location but are not considered as part of their inventory until sold
-
Payment is made by the customer only for the goods that are sold
consignment Paying for the consumed or used material from a stock using movement type 411
9. what are the differences between logistics and SCM?
- Logistics focuses on the efficient and cost-effective delivery of goods to the customer. Supply chain management (SCM) controls the development of raw materials into finished goods that move from the supplier to producer to warehouse to retailers and/or consumers.
- Logistics focuses on the movement and storage of goods, while supply chain management involves the coordination of all activities involved in sourcing, procurement, production, and delivery of products.
-
Logistics deals with the physical flow of goods, including transportation, warehousing, and distribution.
-
Supply chain management encompasses a broader range of activities, including procurement, production planning, inventory management, and customer service.
-
Logistics is a subset of supply chain management, focusing on the execution of the supply chain activities.
-
Supply chain management involves strategic decision-making to optimize the entire supply chain network.
-
Example: Logistics would involve managing the transportation of goods from a warehouse to a retail store, while supply chain management would involve coordinating the sourcing of raw materials, production planning, and distribution to multiple retail locations.
10. How to configure the Master data configuration?
We can config Master data configuration using Material master
11. Explain more details about the Data migration concept in detail.
The data migration concept involves transferring data from one system to another while ensuring data integrity and accuracy.
-
Data extraction from the source system
-
Data transformation and mapping to target system
-
Data loading into the target system
-
Validation and reconciliation of migrated data
-
Testing to ensure data accuracy and completeness
12. Can we define a plant in different ways and if yes How?
A plant can be defined in different ways based on its physical location, organizational structure, or production process.
-
Physical location: A plant can be defined as a physical facility or site where production or distribution activities take place. For example, a manufacturing plant or a warehouse.
-
Organizational structure: A plant can also be defined as a distinct organizational unit within a company. It can represent a specific department or division responsible for certain activities. For example, a sales plant or a purchasing plant.
-
Production process: A plant can be defined based on the type of production process it follows. It can be a discrete manufacturing plant, a process manufacturing plant, or a repetitive manufacturing plant.
-
Different ways of defining a plant can be used to assign specific responsibilities, control access to data, or manage production processes efficiently.
13. Explain about Procure to pay process
The procure to pay process involves acquiring goods or services from a vendor, creating a purchase order, receiving the goods, and making payment.
-
Vendor selection and negotiation
-
Purchase requisition creation
-
Purchase order creation
-
Goods receipt and inspection
-
Invoice verification
-
Payment processing
14. Where did u fund the header table for po
The header table for PO can be found in the SAP MM module.
-
The header table for PO is usually named EKKO.
-
It stores general information about the purchase order, such as the vendor, purchasing organization, and currency.
-
Other related tables include EKPO for item details and EKET for delivery schedules.
-
The header table can be accessed through transaction codes like ME23N or SE16N.
-
Data in the header table can be used for reporting, analysis, and tracking of purchase orders.
15. Explain about MM WM integration
MM WM integration refers to the seamless flow of materials from procurement to storage and distribution.
-
MM manages procurement, inventory management, and invoice verification
-
WM manages the storage and distribution of materials
-
Integration ensures real-time visibility of inventory levels and movement
-
Example: When a purchase order is created in MM, the material is automatically updated in WM for storage and distribution
-
Example: When a material is received in WM, the inventory levels are automatically updated in MM
16. What is an outbound delivery
An outbound delivery is a document that contains all the relevant information for the delivery of goods from a company to a customer.
-
An outbound delivery is created when goods are ready to be shipped to a customer.
-
It includes details such as the delivery date, shipping address, and the items being shipped.
-
The outbound delivery document is used to track the movement of goods from the company's warehouse to the customer's location.
-
It is an important step in the order fulfillment process.
-
For example, when a customer places an order for a product, the company creates an outbound delivery to initiate the shipment of the product to the customer.
17. Explain batch processing
Batch Management in SAP is to create the batch of the material if we have a material that is in two or three different colors so, in this case, we can maintain the batch for the same material in different batches..
Steps to create Batch.
1) We have to create a class using class type 023
2) We have to create Characters for three different colors & assign them to the class.
3) We have to create a PO Using Batch and save.
18. What are the methods of PR creation
PR Creation can create through the following ways
-
Manual creation me51n
-
While performing STO sales orders generates PR number automatically based on the Item category TAS in the sales order
-
Based on the configuration MRP run can generate the PR number
19. What is the master data of MM
Master data means: the data that we shouldn't or can't change for a long time is called master data.
- Material master data
- Vendor master data
- Quota arrangement
- Source list
- Condition master
- Batch master
- Infor record
20. 161 movement type in GRN
161 movement: consumer some particular vendor purchase order to the maximum quantity of product but physically not for mismatch lower quantity stock the customer mail to carving issues to vendor side convening message return to the MIGO material cancelation process
- Good material received and return copy sign and stamp return to vendor and SAP software GRN done
- 161 is used when you return goods to a vendor against a Purchase Order for unknown reasons
- return to the vendor with the help of po
21. what are return deliveries to the vendor concerning returns PO
Return materials to vendor despite payment already paid to the vendor for the procured materials. At the time of goods receipt movement, type 161 will come automatically because we are doing goods receipt against the return purchase order.
Migo - movement 161 t- code
- 122 before invoice
- 161 after invoice return delivery
To return deliveries to a vendor regarding returns PO in SAP MM, follow these steps:
-
Create a returns purchase order (PO) referencing the original purchase order
-
Create a return delivery using transaction code VL10B
-
Enter the returns PO number as a reference in the return delivery
-
Post the return delivery to complete the process
22. What are the Movement types for GR blocked stock?
- 103 - GR into GR blocked stock
- 105 - GR blocked stock to warehouse
Movement type 103 is used for GR-blocked stock in SAP MM.
-
Movement type 103 is used to transfer materials from quality inspection stock to unrestricted stock.
-
GR blocked stock is a special stock category used for materials that have been received but are not yet available for use.
-
By using movement type 103, the materials are released from inspection and made available for use.
-
This movement type helps in maintaining accurate inventory levels and tracking the status of materials in the warehouse.
23. What are Prerequisites for auto PO and ERS
Auto PO and ERS require specific prerequisites for successful implementation.
-
Vendor master data must be maintained accurately
-
Material master data should be updated regularly
-
Purchase info records should be created for automatic PO generation
-
Configuration settings for automatic PO and ERS must be properly maintained
24. How to change material type?
we can change material type by T code MMAM
Material type can be changed in SAP MM by using transaction code MM02.
-
Go to transaction code MM02
-
Enter the material number for which you want to change the material type
-
Navigate to the 'Basic Data 1' tab
-
Change the material type field as required
-
Save the changes
25. What is the field in Material master data that will trigger STO
Material master data is a Special Procurement key
The field in Material master data that triggers STO is the Plant field.
-
The Plant field in Material master data determines the plant location from which the material will be sourced for the STO.
-
When creating a Stock Transport Order (STO), the system uses the Plant field in the Material master data to determine the supplying plant.
-
The Plant field is crucial for setting up the correct supply chain process for STOs.
26. What is the Central Purchase Organisation?
Centralized purchase organization means it can support procurement activities for the plants, which are related to multiple company codes. In this case, no need to assign any company code to the purchase organization and only assign all the plants related to the different company codes.
A purchasing organization is an organization unit under a company or plant that is responsible for procurement activity.
27. What is a credit memo? When is it used?
It is the type of invoice transaction that is used to gate payment revers back from the vendor.
A credit memo is the reduction of the receivable amount paid to the customer. IF THE PRICE IS TOO HIGH.
More Details:
A credit memo is a document issued by a seller to a buyer, indicating a reduction in the amount owed due to returns, discounts, or other reasons.
-
A credit memo is used to correct errors in invoices or to provide refunds to customers.
-
It is typically issued when goods are returned by the customer or when there is a pricing discrepancy.
-
Credit memos can also be used to adjust the amount owed by a customer for future purchases.
-
They are important for maintaining accurate financial records and ensuring customer satisfaction.
-
Examples of credit memo usage include issuing a credit for damaged goods, granting a discount for late delivery, or correcting an overcharge.
28. what is Batch Management?
- Use Materials, such as chemical and pharmaceutical products, require a precise identification of a production lot.
- If the material is managed in batches, both the batch number and the material number serve to identify the product. The system uses this identification scheme to manage these types of stocks.
- When a material in a plant is identified as a batch material, each quantity of the material must be assigned a batch number.
- Whenever a goods movement takes place, you must specify the: Material number Batch number Prerequisites To be able to manage the batch materials in your system, the Batch Management (LO-BM) component must be active in your system.
- Features The batch master record and the batch stock data can be created automatically when a goods receipt for the material is posted in the Materials Management (MM) component.
- You do not have to create this data manually. If the system creates an inspection lot as a result of the goods movement, the batch is automatically recorded in the inspection lot.
29. What is Enterprise Sector?
The enterprise sector refers to the segment of the economy that consists of businesses and organizations engaged in commercial activities.
-
It includes both private and public enterprises.
-
These enterprises produce goods and services for profit or to fulfill a social mission.
-
Examples include manufacturing companies, financial institutions, government agencies, and non-profit organizations.
-
The enterprise sector plays a crucial role in economic growth and development.
-
It encompasses various industries and sectors, such as retail, healthcare, technology, and agriculture.
30. If you have a added customized field in materials, will it be visible in the field selection configuration
Yes, the customized field will be visible in the field selection configuration.
-
Customized fields can be added to the field selection configuration in SAP MM.
-
The field selection configuration allows users to control which fields are visible and editable in various transactions.
-
By adding the customized field to the field selection configuration, it can be made visible and editable as needed.
31. what do you mean by SAP mm what is the purchase order what is sub contracting vendor what moment type used in sub contracting, what is physical inventory
SAP MM is a module that deals with material management. A purchase order is a document used to procure goods or services. A subcontracting vendor is a vendor who provides goods or services to a company. Movement types are used in sub-contracting to track the movement of goods. Physical inventory is a process of counting and verifying the inventory on hand.
-
SAP MM deals with material management
-
A purchase order is a document used to procure goods or services
-
A subcontracting vendor is a vendor who provides goods or services to a company
-
Movement types are used in sub-contracting to track the movement of goods
-
Physical inventory is a process of counting and verifying the inventory on hand
32. What is SAP MM
SAP MM (Materials Management) is a module in the SAP ERP system that manages procurement and inventory functions.
-
Manages procurement processes such as purchase requisitions, purchase orders, and goods receipts
-
Handles inventory management including material storage, movement, and valuation
-
Integrates with other SAP modules like SD (Sales and Distribution) and PP (Production Planning)
33. What are the Types of Invoice Posting
Types of invoice posting include standard invoices, credit memos, and subsequent debits.
-
Standard invoice: Regular invoice for goods or services received.
-
Credit memo: Document issued to reduce the amount owed by a customer.
-
Subsequent debit: Additional charges are added to an invoice after it has been posted.
34. Explain the MRP Process flow
MRP Process flow involves determining material requirements, creating procurement proposals, and converting them into purchase orders.
1. Determining material requirements based on demand forecasts and stock levels
2. Creating procurement proposals for purchasing required materials
3. Converting procurement proposals into purchase orders for suppliers
4. Monitoring and tracking the delivery of materials to ensure timely availability
35. Explain P2P Process
The P2P Process is the Procure Pay process which involves purchasing goods or services from a vendor and making payment for them.
-
The P2P process starts with creating a purchase requisition based on the need for goods or services.
-
The next step is to create a purchase order to specify the details of the purchase, such as quantity, price, and delivery date.
-
Goods or services are received from the vendor and the receipt is recorded in the system.
-
The invoice is received from the vendor and matched with the purchase order and receipt.
-
Payment is made to the vendor based on the invoice.
-
Finally, the process is completed with reconciliation and closure of the purchase order.
36. What is the difference between S4 Hana and ECC
SAP S/4HANA is the next-generation business suite from SAP, built on the advanced in-memory platform, while ECC is the traditional ERP system.
-
SAP S/4HANA is built on the SAP HANA platform, providing real-time analytics and processing capabilities, while ECC is not.
-
SAP S/4HANA offers a simplified data model and user interface, enabling faster decision-making and innovation, while ECC has a more complex data model and user interface.
-
SAP S/4HANA supports advanced technologies like machine learning, IoT, and blockchain, while ECC does not have native support for these technologies.
-
SAP S/4HANA is designed for the digital economy, with features like embedded analytics, AI, and automation, while ECC is more suited for traditional business processes.
-
SAP S/4HANA offers a cloud-first approach with options for on-premise, cloud, or hybrid deployments, while ECC is primarily an on-premise solution.
37. What are the scheduling agreement
this is also called Open purchase order in which we fix the date and quantity of the goods receving.
Scheduling agreements are long-term agreements with vendors for the supply of materials or services.
-
Scheduling agreements outline the terms and conditions for the supply of materials or services over a specified period of time.
-
They can include details such as delivery schedules, pricing, and quantities to be supplied.
-
Scheduling agreements help in planning and managing procurement activities efficiently.
-
Example: A company enters into a scheduling agreement with a vendor to receive monthly shipments of raw materials for production.
38. How to measure scale in purchasing order
Scale in purchasing order can be measured by the quantity of items ordered and the total cost of the order.
-
The quantity of items ordered can be used to measure scale in purchasing order.
-
The total cost of the order can also be used to measure scale in purchasing order.
-
Other factors such as the frequency of orders and the number of suppliers can also be considered.
-
For example, if a company orders 1000 units of a product at a cost of $10 per unit, the scale of the purchasing order would be 1000 x $10 = $10,000.
39. Explain P2P and O2c cycle
P2P and O2C are two important cycles in SAP MM. P2P refers to Procure-to-Pay and O2C refers to Order-to-Cash.
-
P2P cycle involves procurement of goods and services from external vendors
-
O2C cycle involves sales of goods and services to customers
-
P2P cycle includes steps like purchase requisition, purchase order, goods receipt, and invoice verification
-
O2C cycle includes steps like sales order, delivery, billing, and payment receipt
-
Both cycles are closely linked and impact each other
40. Explain the complete P2P cycle. 2- Explain the complete STO process with T-code.
SAP Procure to Pay process is required when we need to purchase materials/services from an external vendor for our company. This process includes all the business tasks starting from a purchase requisition (PR) and finishing with payment to the vendor.
- PR-ME51N
- RFQ-ME47
- VENDOR EVULATION-ME49
- PO-ME21N
- MIGO-GR101
- MIRO
The P2P cycle involves the entire procurement process from requisition to payment. STO process is the transfer of goods between two plants within a company.
-
P2P cycle: Requisition -> Purchase Order -> Goods Receipt -> Invoice Verification -> Payment
-
STO process: Create STO -> Delivery -> Goods Receipt -> Invoice Verification
-
T-code for STO process: ME21N (Create STO), VL10B (Delivery), MIGO (Goods Receipt), MIRO (Invoice Verification)
41. Have you worked on any interfaces ?
Yes, I have worked on interfaces in my role as an SAP MM Consultant.
-
I have experience in integrating SAP MM with other modules like SAP SD and SAP FI.
-
I have worked on setting up and configuring IDocs for data exchange between SAP systems.
-
I have also worked on integrating SAP MM with external systems using technologies like EDI and XML.
-
I have experience in mapping and transforming data between different systems.
-
I have worked on troubleshooting and resolving interface issues.
-
I have knowledge of SAP PI/PO for middleware integration.
-
I have experience in working with BAPIs and RFCs for interface development.
42. What is a Purchase Order?
A Purchase Order is a document issued by a buyer to a seller, outlining the details of goods or services to be purchased.
-
It is a legally binding document
-
Includes details such as quantity, price, delivery date, and terms of payment
-
Used to track and manage purchases
-
Can be created manually or automatically in SAP MM
43. Define Physical inventory
Physical inventory is the process of counting and verifying the actual quantity of goods in stock.
-
Physical inventory involves physically counting and inspecting the items in a warehouse or storage location.
-
It helps in identifying any discrepancies between the actual stock and the recorded stock in the system.
-
The process may include using barcode scanners, RFID technology, or manual counting methods.
-
Physical inventory is usually conducted periodically or during specific events like year-end closing.
-
It ensures accurate inventory records, helps in identifying stock shortages or excess, and aids in financial reporting.
44. Explain STO process
STO process is a method used in SAP MM to transfer stock between different plants within the same company code.
-
STO stands for Stock Transport Order.
-
It involves creating a purchase order in the supplying plant and a corresponding sales order in the receiving plant.
-
The goods are then transferred from the supplying plant to the receiving plant using the delivery process.
-
The receiving plant receives the goods and posts the receipt of the goods.
-
The supplying plant then receives the payment for the goods through the billing process.
45. What are Tcodes for transactions?
Tcodes are transaction codes used in SAP to execute specific functions.
T code transaction OBYC
-
MM01 - Create Material Master
-
ME21N - Create Purchase Order
-
MIGO - Goods Movement
-
MB51 - Material Document List
-
ME23N - Display Purchase Order
46. What is the standard purchase organization
Standard purchasing organization is mainly used for special procurement process.
Configuration steps to assign standard purchasing organization to plant in SAP is
SPRO>IMG>Enterprise Structure>Assignment>Materials Management>Assign
Standard Purchasing Organization to Plant.
47. How to define consignment stock
Consignment stock is inventory that is owned by the supplier but stored at the customer's location until it is used or sold.
-
Consignment stock is owned by the supplier but stored at the customer's location.
-
The supplier retains ownership until the stock is used or sold.
-
The customer only pays for the stock when it is used or sold.
-
Consignment stock can help reduce inventory costs for both the supplier and customer.
-
Examples of consignment stock include vending machines and retail displays.
48. What is vendor master data?
Vendor master data is information about vendors stored in the system for procurement purposes.
-
Contains details such as vendor name, address, contact information, payment terms, etc.
-
Used in procurement processes to facilitate communication and transactions with vendors.
-
Helps in maintaining accurate records of vendor interactions and transactions.
-
Can include information on vendor performance, certifications, and compliance.
-
Example: Vendor code, vendor name, vendor address, payment terms.
49. What is the vendor account group?
Vendor account groups differentiate the type of vendor by giving different number series Account group.
1) 0001
2) LIEF
50. How many ways to create a purchase order?
1) we can create po concerning pr
2) PO concerning RFQ
3) PO concerning the contract agreement
4) PO concerning the scheduling agreement
5) po concerning po ( me21n)
There are multiple ways to create a purchase order in SAP MM.
-
Purchase orders can be created manually using transaction code ME21N.
-
Purchase order can be created automatically through a requisition using transaction code ME59N.
-
A purchase order can be created from a purchase requisition using transaction code ME21N.
-
Purchase order can be created from a contract using transaction code ME31K.
-
Purchase order can be created from a scheduling agreement using transaction code ME38.